Cas pratique : L’électroérosion par fil comme alternative pour l’usinage de rainures de disque de turbine pour le secteur aéronautique.
ONA a réalisé une étude afin d’analyser le processus d’électroérosion de découpe par fil (WEDM) comme alternative à l’usinage conventionnel (brochage) des rainures de disques de turbines pour le secteur aéronautique.
\ L’Éélectroérosion pour l’usinage de rainures de disque de turbine
\ Être leader du secteur de l’électroérosion n’est possible qu’avec un travail continu de recherche de nouvelles technologies et d’applications, afin d’apporter des solutions avancées adaptées aux besoins des clients. ONA est un exemple clair d’entreprise orientée vers l’innovation. Ses 65 ans d’expérience dans la fourniture des meilleures technologies d’électroérosion en témoignent. Conformément à cette philosophie, l’entreprise basque a réalisé une étude afin d’analyser le processus d’électroérosion de découpe par fil (WEDM) comme alternative à l’usinage conventionnel (brochage) des rainures de disques de turbines pour le secteur aéronautique. L’électroérosion par fil de rainures de disques de turbine pourrait de fait devenir une option industrielle viable pour le brochage à l’avenir.
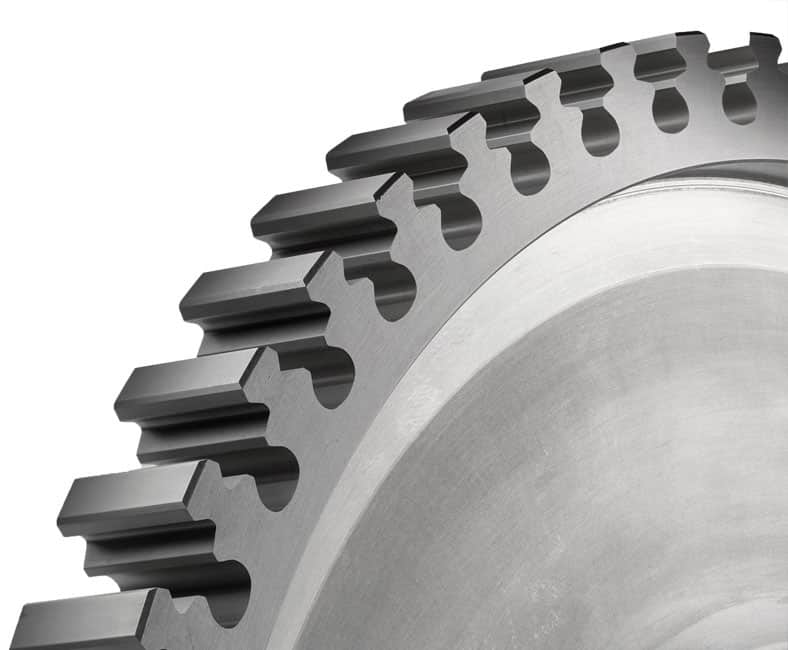
\ Hypothèse et méthode
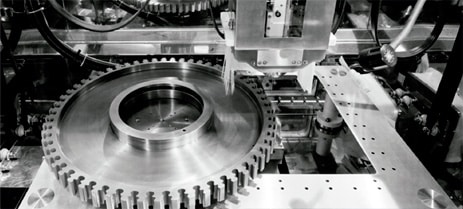
Dans sa recherche, ONA a comparé le processus d’électroérosion avec des procédés d’usinage plus traditionnels tels que le brochage et le fraisage. Points clés de sa recherche, ONA a comparé des paramètres tels que les exigences d’intégrité superficielle, de précision et de temps d’usinage des rainures d’insertion des aubes.
Un disque de turbine présentant les caractéristiques suivantes a été découpé pour le test :
Matériau : Inconel 718.
Diamètre extérieur : 350 mm.
28 rainures.
Rainures de disque de turbine en angle de 30 degrés.
82 mm d’épaisseur.
Tolérance de profil 0,01 mm.
Tolérance de positionnement angulaire radial 0,08 mm.
L’objectif de cette recherche était de découper les dents du firtree de la turbine à l’aide de la technologie d’électroérosion de découpe par fil, pour répondre aux exigences de tolérance et ainsi analyser les informations suivantes :
- Temps de dégrossissage d’un profil complet.
- Temps de finition d’un profil complet.
- Temps total d’érosion d’un profil complet.
- Temps total de dégrossissage du disque de turbine (y compris le temps de préparation).
- Temps total de finition du disque de turbine (y compris le temps de préparation).
- Temps total d’usinage (y compris le temps de configuration).
- Capacité d’enlèvement de matière MMR (mm2/min).
- Épaisseur de la couche de matière refondue.
\ Configuration et conditions d’usinage EDM
L’analyse a utilisé la technologie ONA standard pour l’alliage de nickel, à savoir un plateau rotatif à deux axes dans deux conditions de nettoyage différentes. De bonnes conditions de lavage (buses fermées) d’une part, et des conditions de nettoyage moindres (buses ouvertes) d’autre part. Un fil recouvert de 0,25 a en outre été utilisé pour la découpe de dégrossissage.
Ces deux scénarios choisis pour l’étude (buses ouvertes et fermées) ont permis de réaliser différents tests afin d’évaluer le meilleur temps d’érosion, celui-ci dépendant largement des conditions de nettoyage. Les caractéristiques géométriques des disques de turbine ont parfois empêché l’utilisation de l’électroérosion avec des buses fermées. Il s’agit de modèles particulièrement utiles pour la fabrication de moules de grandes dimension et avec différentes cavités, soit exactement la spécialité de Concours Mold.
\ Résultats de la recherche
Les résultats des tests ont montré que la technologie d’électroérosion par fil permettait d’obtenir une épaisseur de couche refondue d’une plage de microns nécessaire (environ 5 µm) et une précision suffisante dans les rainures d’insertion des aubes, avec une tolérance de 0,01 mm. Ces résultats ont été obtenus après un passage de dégrossissage et deux passages de finition (stratégie de 3 coupes).
Dans des conditions de nettoyage moindres (buses ouvertes), la capacité d’enlèvement de matière par le dégrossissage est de 110 mm2/min. De fait, la capacité d’enlèvement de matière pour la stratégie utilisée dans la recherche (un passage de dégrossissage et deux passages de finition), s’est élevée à 60 mm2/min.
Dans de bonnes conditions de nettoyage (buses fermées), on observe en revanche une amélioration significative de la capacité d’enlèvement de la matière. Pour le seul dégrossissage, elle atteint plus de 400 mm2/min.
\ Commentaires basés sur les résultats obtenus
La plupart des disques de la turbine ont des profils d’angle compris entre 5 et 30 degrés. La fonction de découpe conique de la machine d’électroérosion par fil ONA permet d’obtenir de bons résultats en matière de précision géométrique pour des profils de moins de 10 degrés. Pour des angles plus importants, il est recommandé d’utiliser un plateau rotatif à deux axes.
Pour obtenir l’élimination de la matière souhaitée et améliorer les temps d’usinage, il est essentiel de nettoyer le diélectrique dans la zone d’érosion. Le maintien de la fermeture de la plupart des buses dans le profil est essentiel. Pour des disques de turbine de plus petit diamètre (lorsque les buses interfèrent avec le dispositif de fixation), l’utilisation de buses spéciales est recommandée.
L’utilisation de fils recouverts est enfin également recommandée pour réduire le processus d’électroérosion par fil, notamment dans la découpe de dégrossissage.
\ Conclusions
Cette recherche nous a permis de conclure que l’électroérosion par fil de profils de disques de turbine est une alternative très viable pour concurrencer le brochage comme solution industrielle dans le secteur aéronautique. La dernière génération de générateurs, de plus en plus puissants, et les commandes numériques les plus avancées, permettent d’optimiser le temps d’usinage et de réduire l’épaisseur de la couche blanche. Ils offrent également une très bonne précision géométrique.
Dans l’étude réalisée par ONA (stratégie à 3 découpes), l’usinage de rainures de disques de turbine respecte les tolérances géométriques avec obtention d’une couche blanche inférieure à 5 μm. Des informations précieuses ont en outre été obtenues sur la capacité d’enlèvement de matière et le temps d’usinage.
Il est vrai que la certification de l’ensemble du processus d’usinage par électroérosion, selon les normes aéronautiques, peut s’avérer long et coûteux. ONA en conclut pour cette raison que la meilleure option est de combiner l’électroérosion par fil, plus économique et rapide, pour le dégrossissage, et le brochage pour la finition. La re-certification du processus n’est ainsi pas nécessaire.